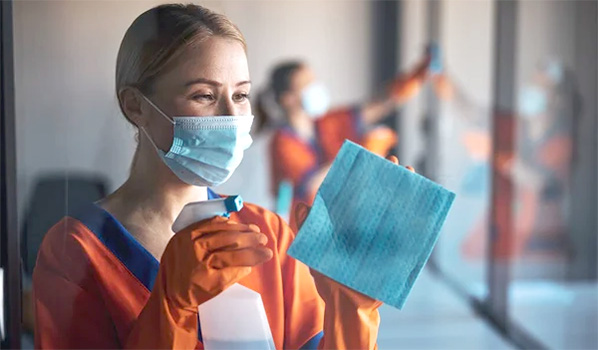
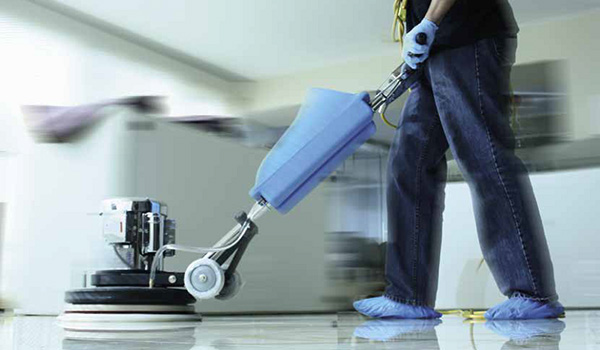
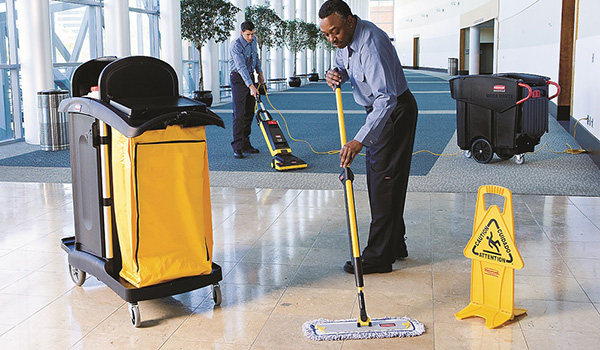
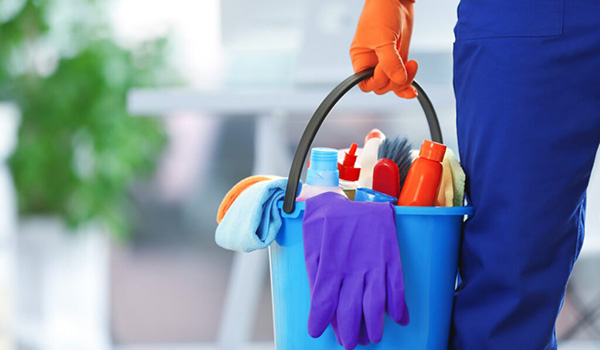
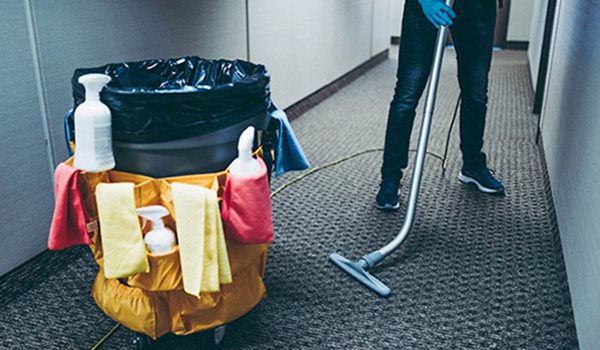
Services Offered
Janitorial Division
- Full service janitorial
- Janitorial supplies / paper products
- Full service floor & carpet cleaning
- Day Porter service
- Construction clean-up
- Pressure washing
- Window washing
- Parking lot sweeping
- Clean room / Vivarium cleaning
Specialty Division
- Detailed disinfection of high trafficked areas
- Detailed sanitation of bathrooms
- Detailed disinfection/sanitation of office spaces
(some exclusions apply)
Floor Division
- Hard surface floor maintenance
- Vinyl and VTC refinishing
- Marble honing and polishing
- Tile and stone restoration
- Wood sanding, screening, and recoating
- Concrete cleaning, refinishing, and sealing
- Grout cleaning
- Carpet maintenance (biodegradable)
- Emergency flood-water extraction
- Hot water extraction
- Steam cleaning
- Rotary (bonnet) dry cleaning
- Upholstery cleaning
- Partition cleaning
- Carpet installation
- Carpet re-stretching & repair
- Pressure washing
Construction Division
- Drywall installation
- Electrical Work
- Painting
- Installation and removal of carpets
- Installation and removal of tile and stone
- Renovations
- New construction
- Repairs
- Roofing
- Carpentry
- Additions and remodels
- Flooring and hardwood installation
- Windows and doors
- Concrete, brick and stone
- Carpet repairs
Operational Excellence Through OS1
At JFS Facility Solutions our process is based on a systematic approach with a philosophy that there is one best way to perform any work. Working with worldrenowned consultants over the past 15 years, we employ a program of service specialists that have exact training and performance standards that simplify complex scheduling and work tasks to meet our customer’s expectations with consistency and competence.
JFS uses the Manage Men™ Operating System One or (OS1) ®. This process-based, environmentally sustainable approach to cleaning is employed by some of the largest and most prestigious universities and corporations in the world including Lockheed Martin, University of Texas, the Boeing Company, University of North Carolina, QUALCOMM, Sandia Laboratories and the University of Massachusetts.
At the core of the philosophy are the concepts that we “Clean for Health First and Then Appearance” and that emphasis be placed on “Treating Cleaning Workers as First Class Citizens”. The philosophy also emphasizes exceeding safety regulations and performing cleaning while minimizing environmental harm.
Our Key to Success
- Reduce waste and misuse of cleaning products
- Professionalize the cleaning function
- Reduce non-recycled consumable supply consumption annually
- Increase training and education for cleaning workers
- Support facility owners and managers seeking LEED certifications and other accreditations
- Implement inventory systems of cleaning materials to ensure that chemicals purchased are used correctly
- Submit to rigorous outside third party auditing of cleaning processes
- Benchmark best practices
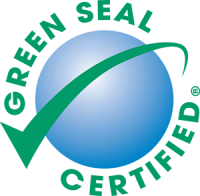
Cleaning Practices
Source Reduction
Our chemical packaging is shipped in pre-measured Pac’s that consist of high concentration, rule of one, dilution ratio end use. This reduces pollution by not shipping large quantities of water in high dilution ratio products. It reduces product packaging to landfills and reduces storage space requirements.
Specialist System
All jobs tasks are divided into four specialists who are assigned specific equipment and move systematically throughout the building creating labor efficiencies, enhanced quality, energy savings, and increased safety. The Restroom, Light Duty, Utility, and Vacuum Specialists have well defined roles with checks and balances incorporated into the building work load which dramatically improves quality.
Chemical Usage Tracking
Chemical usage is tracked on a daily basis through the solution and filter log book to ensure that only the proper amount of product is being issued, consumed and used correctly each day.
Chemical Compound Reductions and GS 37 Chemicals
Daily cleaning is done with three base products for
ninety-five percent of our tasks rather than twenty
plus products which is typical in the JanSan industry.
We employ the use of GS 37 formulated products.
Outside Third Party Audits
Each year we extend the opportunity for our customers
to participate in third party process audits. For a
nominal fee, a facility can be audited for compliance
to standard process and practices. This third party
audit also benchmarks organization and facilities
agains others nationwide and gives practical feedback.
Those organizations that achieve the standards
set for excellence or a green certification are recognized
annually with press releases and nationally
recognized awards.
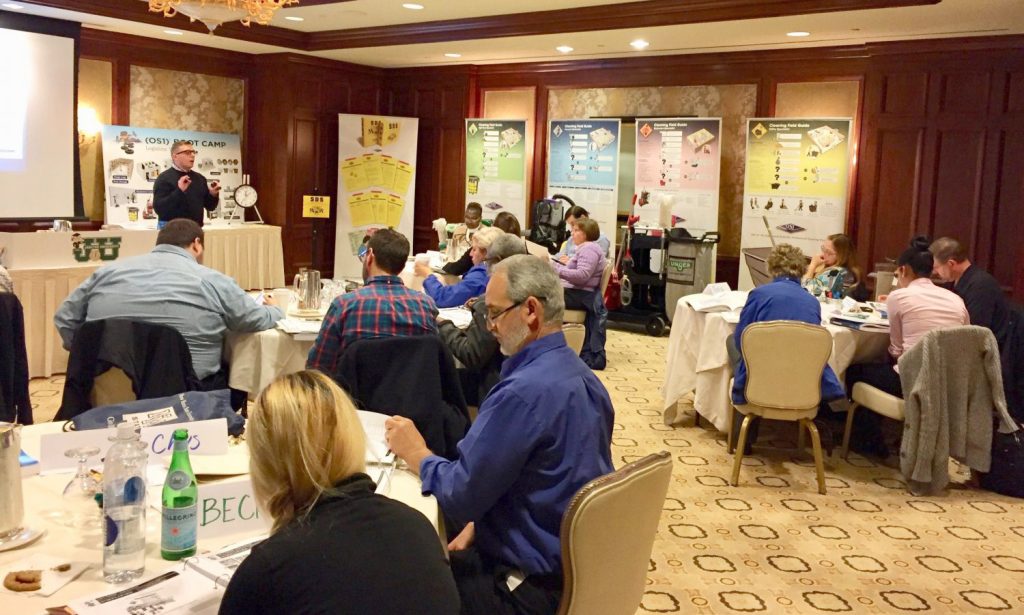
Training That Pays
Our company has a strong belief in continual education and training to provide the opportunity for employees to be promoted from within the company as their knowledge and skill levels increase.
All our managers, field supervisors, and project managers take a week-long course at Janitor University in Utah. JFS also provides training for all employees in our “state of the art” Operating System One (OS1) specified training classroom as well as conducting on-site clone training.
Further education is available through our own JFS University including certifications in each of the specialist functions and various other certifications available through ManageMen, BSCAI and ISSA.